Andrew Carnegie’s transition from poverty to philanthropy illustrates how determination and hard work can transform lives. Hailing from Scotland, he moved to the United States at the age of 13, taking on a variety of jobs to provide for his family. Through his unwavering determination and strategic investments, he founded Carnegie Steel, a dominant force in the industry. Despite his success, Carnegie believed that wealth should be utilized for the greater good. In his later years, he devoted himself to philanthropic endeavors, supporting the establishment of numerous libraries and educational institutions. His legacy serves as a source of inspiration for contemporary philanthropy, underscoring the obligation of the affluent to uplift society. To learn more about his lasting impact on philanthropy, visit this link.
Key Takeaways
- Carnegie's modest beginnings in Scotland shaped his relentless drive for success and strong work ethic.
- Strategic career shifts and early investments led to the accumulation of significant wealth in the U.S.
- Founding Carnegie Steel revolutionized the steel industry through innovative techniques and vertical integration.
- His philanthropic philosophy emphasized the responsibility of the wealthy to invest in education and community development.
Early Life in Scotland

Born in Scotland, Andrew Carnegie's early life was marked by modest beginnings that shaped his future ambitions. You can imagine the struggles his family faced, living in a cramped two-room apartment above a weaving shop.
At just 13, he immigrated to the United States, where he quickly learned the value of hard work. Starting as a bobbin boy in a cotton mill, you see him earning a mere $1.20 a week.
But Carnegie didn't stop there; he seized opportunities, becoming a messenger for a telegraph company. This role sparked his self-education in telegraphy, laying a solid foundation for his future.
His experiences in Pittsburgh instilled a relentless drive that propelled him toward greater aspirations and inevitable success.
Journey to Wealth

After establishing a strong work ethic in his early years, Carnegie quickly capitalized on opportunities that led him to immense wealth.
You'll see how his journey unfolded through strategic career shifts. Starting as a bobbin boy, he learned the value of hard work. Shifting to a messenger, he honed his skills in telegraphy, which opened doors at the Pennsylvania Railroad.
Here, he gained insights into investments that would shape his future. His early investments in companies like Adams Express and oil wells during the Civil War provided financial groundwork.
Founding Carnegie Steel
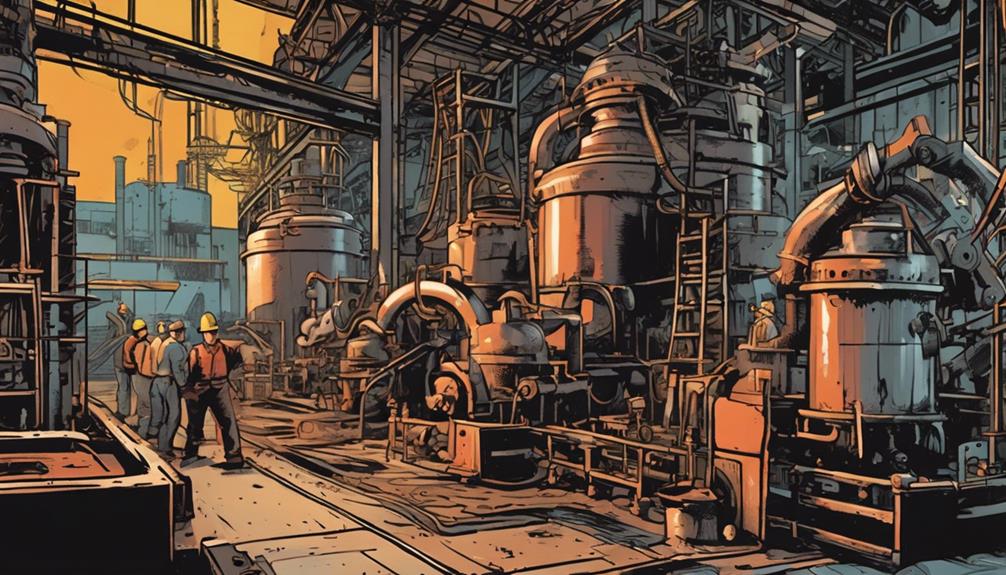
Carnegie founded Carnegie Steel by applying innovative techniques like the Bessemer process and embracing vertical integration to revolutionize the steel industry. This approach not only improved efficiency but also considerably reduced production costs. By controlling the supply chain, from raw materials to transportation, you helped create a dominant enterprise in steel manufacturing.
Technique | Description | Impact |
---|---|---|
Bessemer Process | A method to produce steel quickly and cheaply | Increased production capacity |
Vertical Integration | Control over all production stages | Enhanced efficiency and reduced costs |
Skilled Workforce | Hiring talented laborers | Improved product quality |
Strategic Partnerships | Collaborating with railroads | Expanded distribution networks |
Innovation | Investing in research and development | Fostered continuous improvements |
Philanthropic Philosophy

Philanthropy became Andrew Carnegie's guiding principle, reflecting his belief that the wealthy have a responsibility to use their fortunes for the greater good of society.
You'd find that Carnegie viewed excessive wealth as a tool for social improvement, not just personal gain. He argued in 'The Gospel of Wealth' that dying rich was a disgrace; instead, he encouraged living modestly while promoting benevolent causes.
Carnegie believed in investing in education and public libraries, seeing access to knowledge as essential for societal advancement. His philosophy emphasized the importance of creating lasting impacts rather than temporary reliefs.
Major Contributions and Initiatives
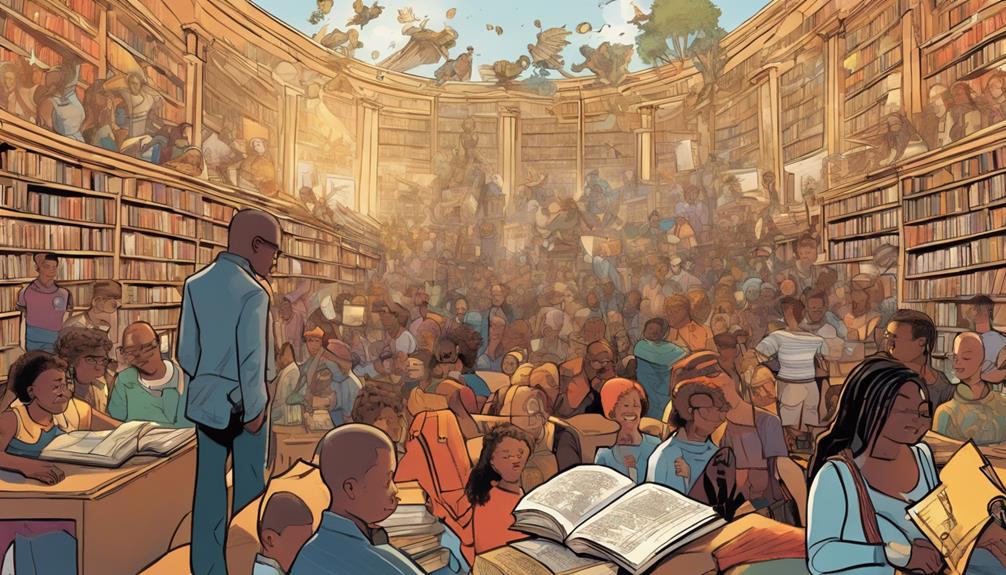
Among Andrew Carnegie's most significant contributions are the thousands of libraries and educational institutions he funded, which transformed access to knowledge for countless individuals.
You'll find that Carnegie established over 2,500 public libraries across the United States, ensuring communities had free access to books and resources. He also invested heavily in colleges and universities, enhancing educational opportunities for students.
His commitment to education led to the founding of institutions like Carnegie Mellon University, which continues to thrive today. Additionally, Carnegie's initiatives extended to cultural organizations, promoting the arts and sciences.
Lasting Legacy

The impact of Carnegie's contributions continues to resonate, shaping the domains of education and philanthropy in ways that still benefit society today.
His establishment of libraries and educational institutions laid the groundwork for accessible learning, fostering a culture of knowledge-sharing. You can see his influence in countless public libraries and organizations dedicated to education and arts, which serve communities across the globe.
Carnegie's belief in the responsibility of the wealthy to give back has inspired generations of philanthropists. His legacy reminds you that wealth holds a greater purpose when used to uplift others.
Today, his vision lives on through institutions like Carnegie Mellon University, which embody his commitment to education and public service, ensuring his impact endures well into the future.
Influence on Modern Philanthropy
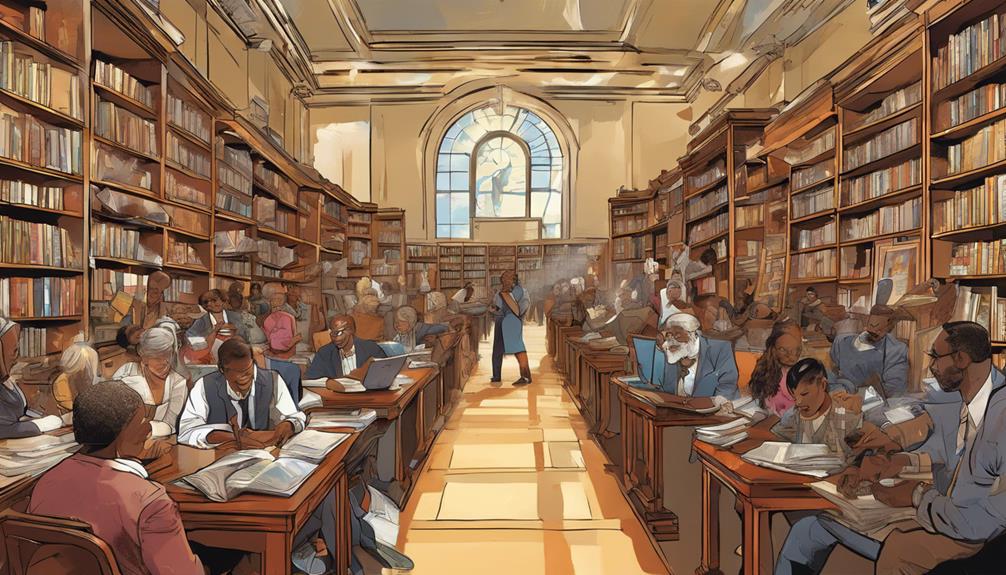
Carnegie's vision for using wealth to benefit society has fundamentally shaped how modern philanthropists approach their giving. His belief in the responsibility of the wealthy to contribute to the public good resonates today, influencing billionaires like Bill Gates and Warren Buffett.
You'll find many contemporary philanthropists adopting a strategic approach to their charitable efforts, often focusing on sustainable change rather than temporary relief. The rise of initiatives like Giving Pledge reflects Carnegie's ethos, encouraging the wealthy to dedicate a significant portion of their fortunes to philanthropy.
Additionally, his emphasis on education and community development continues to inspire funding in these areas, demonstrating that his legacy lives on through modern philanthropic practices, driving societal progress and innovation.
What similarities can be drawn between the philanthropic journeys of Carnegie and Bill Gates?
When comparing the philanthropic journeys of Carnegie and bill gates: visionary philanthropist, several similarities can be drawn. Both men focused on education and public health initiatives, using their wealth to create long-lasting impact. Additionally, they each established prominent foundations dedicated to improving society and addressing global challenges.
Conclusion
As you reflect on Carnegie's journey, picture a bridge stretching from the gritty streets of Pittsburgh to grand libraries and concert halls. Each plank symbolizes his hard work and dedication, connecting wealth to purpose.
Carnegie's life reminds you that fortune isn't just about accumulation; it's about giving back. Just as he transformed steel into structures that shaped a nation, his philanthropy carved pathways for future generations.
This inspires you to contemplate your own role in uplifting society.